Ultimate Overview to Preventing Weld Undercut: Tips and Techniques
Ultimate Overview to Preventing Weld Undercut: Tips and Techniques
Blog Article
Essential Tips for Welders: Protecting Against Undercut Welding and Ensuring Stronger Weld Joints
In the realm of welding, attaining strong and long lasting weld joints is the cornerstone of producing top quality job. One typical obstacle that welders typically come across is undercut welding, which can jeopardize the integrity of the weld joint.

Comprehending Undercut Welding
Undercut welding is a common welding defect that takes place when the weld steel fails to properly fill the groove and leads to a groove-like clinical depression along the weld bead. This problem weakens the weld joint, making it at risk to splitting and failing under stress. Undercutting can be triggered by numerous elements, including too much welding existing, high welding speed, improper electrode angle, incorrect electrode dimension, and bad welding technique.
Among the main factors for undercut welding is an imbalance between the welding present and the welding speed. If the welding current is as well high or the welding speed is as well fast, the weld steel might not appropriately load the groove, bring about damaging. In addition, using an electrode that is as well big can cause a comparable result, as the excess steel can not properly flow into the groove.
To stop undercut welding, welders must guarantee they are utilizing the proper welding criteria, preserve an appropriate electrode angle, choose the ideal electrode size, and practice correct welding techniques. By addressing these factors, welders can minimize the threat of damaging and produce stronger, a lot more reliable weld joints.
Proper Welding Strategy
Effective welding method plays a critical duty in ensuring the top quality and honesty of weld joints. Proper welding method involves a combination of ability, adherence, and precision to ideal practices. One fundamental aspect of proper welding method is maintaining the proper angle and distance between the welding weapon and the work surface. Welders have to likewise pay attention to the travel speed and warmth input to avoid issues like undercutting, porosity, or incomplete combination.
Furthermore, a steady and regular hand motion is necessary for creating strong and resilient weld joints. Welders ought to go for smooth, consistent activities to ensure also circulation of the weld material. Correct control of the welding weapon and filler material is additionally key to attaining ideal penetration and blend.
In addition, managing the warmth input and choosing the suitable welding specifications based on the material being bonded are vital consider accomplishing top quality welds - Preventing weld undercut. Welders need to adhere to the suggested setups provided by welding treatment specifications and change them as needed based upon the certain demands of the task. By grasping correct welding techniques, welders can dramatically enhance the toughness and integrity of their weld joints
Selecting the Right Electrode
Preserving the proper angle and range between the welding weapon and the workpiece is fundamental when thinking about the significance of choosing the ideal electrode in welding applications. The choice of electrode plays a crucial role in identifying the high quality and toughness of the weld joint. Electrodes are available in numerous types, each created for particular objectives and materials.
Firstly, choosing the appropriate electrode size is necessary. Thinner Full Article electrodes appropriate for welding slim products, while thicker electrodes are better for thicker materials and greater heat applications. Matching the electrode size to the thickness of the work surface helps accomplish a well balanced weld.
Secondly, recognizing the material composition of the electrode is important. Different electrodes are made for welding specific materials like steel, stainless-steel, light weight aluminum, or cast iron. Making use of the correct electrode material makes certain great combination and reduces the threat of problems in the weld.
Finally, thinking about the welding placement and method is crucial when selecting the electrode type. For example, certain electrodes are better fit for overhanging or vertical welding positions, while others work well for flat or horizontal settings. Picking the appropriate electrode based on the welding strategy boosts the overall weld top quality and integrity.
Preparing the Base Steel
To guarantee an effective welding process, what initial steps should be taken when preparing the base metal for welding? In addition, any existing weld product or residue from previous welding need to be eliminated to make certain a clean surface area for the new weld.
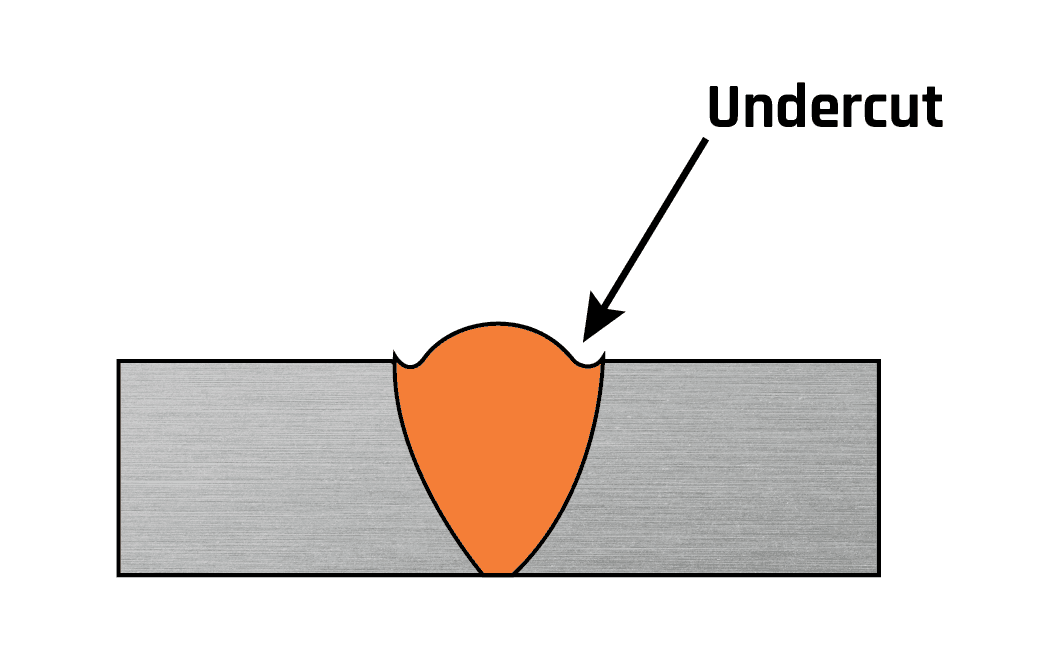
Carrying Out Post-Weld Evaluations
After carrying out these evaluations, welders should contrast the outcomes versus market requirements and task needs to make certain that the weld joint meets all needed criteria. Any type of discrepancies or inadequacies discovered throughout the post-weld examination needs to be immediately attended to via appropriate restorative actions to ensure the weld's honesty. By vigilantly carrying out post-weld look at this site assessments and without delay attending to any type of issues, welders can support the quality and dependability of their job, eventually adding to the safety and longevity of the welded frameworks.
Verdict

To conclude, stopping undercut welding and guaranteeing stronger weld joints call for a combination of correct welding strategy, picking the right electrode, preparing the base steel appropriately, and carrying out post-weld examinations. By understanding the reasons for undercut welding and executing the required safety measures, welders can create high-quality weld joints that satisfy sector requirements and make certain the structural stability of the bonded elements.
Undercut welding is a common welding issue that occurs when the weld metal falls short to correctly fill the groove and results in a groove-like clinical depression along the weld bead (Preventing weld undercut). Undercutting can be triggered by numerous elements, consisting of too much welding present, high welding speed, improper electrode angle, inaccurate electrode size, and inadequate welding strategy
One of the major factors for undercut welding is a discrepancy in between the welding present go to this site and the welding speed. If the welding current is as well high or the welding rate is too quickly, the weld steel might not adequately load the groove, leading to undercutting.Maintaining the proper angle and range in between the welding gun and the work surface is basic when thinking about the importance of choosing the ideal electrode in welding applications.
Report this page